|
|
Electrode Tip Geometry Selection
In AC welding, the electrode is typically balled up and used so there is no tip geometry to prepare. Therefore, this section
is dedicated to DC welding.

Welding should follow an equipment supplier's suggested procedures and dimensions first, because they have usually performed
a lot of qualifying and troubleshooting work to optimize electrode preparation for their equipment. However, where these specifications
do not exist or the welder or engineer would like to change those settings to possibly improve and optimize their welding,
Pro-Fusion offers the following guidelines:
- Electrode Diameter - The welding equipment supplier's recommendations and the American Welding Society recommendations are
the best place to start with this variable. Keep in mind that as you increase the diameter of the electrode you are able to
handle more amperage. For a given amperage, larger diameter electrodes are more difficult to start than smaller ones, but
they will probably erode less rapidly. If you use too large an electrode for your amperage level, you are likely to experience
arc instability.
- Electrode Taper - This is usually called out in degrees of included angle (usually anywhere between 14 degrees and 60 degrees).
Below is a summary chart that illustrates how different tapers offer different arc shapes and features:
Sharper Electrodes |
Blunter Electrodes |
Easy arc starting |
Usually harder to start the arc |
Handle less amperage |
Handle more amperage |
Wider arc shape |
Narrower arc shape |
Good arc stability |
Potential for more arc wander |
Less weld penetration |
Better weld penetration |
Shorter electrode life |
Longer electrode life |
In addition, to demonstrate graphically how the taper selection will effect the size of the weld bead and the amount of penetration,
below is a drawing that shows typical representations of the arc shape and resultant weld profile for different tapers.
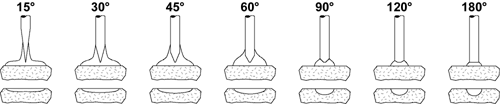
Arc Shape and Fusion Zone Profile as a Function of Electrode Included Angle
The fusion zone profile will also depend on:
- Electrode tip diameter (flat)
- Arc Gap
- Material to be welded
- Shield gas used
- Electrode Tip Diameter - Grinding an electrode to a point is sometimes desirable for certain applications, especially where
arc starting is difficult or short duration welds on small parts are performed. However in most cases it is best for a welder
to leave a flat spot or tip diameter at the end of electrode. This reduces erosion at the thin part of a point and reduces
the concern that the tip may fall into the weld. Larger and smaller tip diameters offer the following trade-offs:
Smaller Tip |
Larger Tip |
Easier arc starting |
Usually harder to start the arc |
Potential for more arc wander |
Good arc stability |
Less weld penetration |
More weld penetration |
Shorter electrode life |
More electrode life |
- - - - - - - - - - - - - - - - - - - - - - - - - - - - - - - - - - - - - - - - - - - - - - - - - - - - - - - - - - - - -
- - - - - - - - - - - - - - - - - - - - - - - - - - - - - - - - - - - - - - - - - - - - - - - - - - - - - - - - - - - - -
- - - - - - - - - - - - - - - - - - - - - - - - - - - - - - - - - - - - - - - - - - - - - - - - - - - - - - - - - - - - -
- - - - - - - - - - - - - - - - - - - - - - - - - - - - - - - - - - - - - - - - - - - - - - - - - - - - - - - - - - - - -
- - - - - - - - - - - - - - - - - - - - - - - - - - - - - - - - - - - - - - - - - - - - - - - - - - - - - - - - - - - - -
- - - - - - - - - - - - - - - - - - - - - - - - - - - - - - - - - - - - - - - - - - - - - - - - - - - - - - - - - - - - -
- - - - - - - - - - - - - - - - - - - - - - - - - - - - - - - - - -
|
|